
DESCRIPTION
Rhino’s Vacuum Assisted Resin Transfer Molding (VARTM) or Liquid Resin Infusion technology is a closed composite manufacturing process in which dry fibers are laid on the tool and vacuum sealed while Rhino 1310T liquid resin and hardener. The resin is pulled into the mould by negative pressure to impregnate the fibers already laid out in the mould. This liquid resin technology provides for lower cost and lower cure temperatures.
Since the liquid resin techniques do not require curing cycles over 60°C, the tooling is much easier to construct. Liquid resin infusion forms a uniform composite of nearly ideal 65% fiberglass to 35% resin by weight.
TYPICAL APPLICATIONS
• Aerospace • High Strength Composites • Resin Infusion
• Aircraft • High Temperature Systems • RTM
• Automotive Repair • Mannequins and Displays • Skis and Snowboards
• Bag Molding • Military Specifications • Tennis Rackets
• Casting • Models • Theme Parks
• Cored Structures • Motorcycle Helmets • Tool And Die Production
• Decoupage Coatings • Movie Sets • Transportation
• Fiberglass Laminating • Polyester Replacement • Vacuum Bagging
• Filament Winding • Potting and Encapsulation • VARTM
• Flexible Membranes • Press Molding • Water Skis and Wakeboards
• Golf Shafts • Prosthetics • Wind Energy Rotor Blades
• Hand Lay-up Laminating • Rapid Prototyping • Wind Surfers and Surfboards
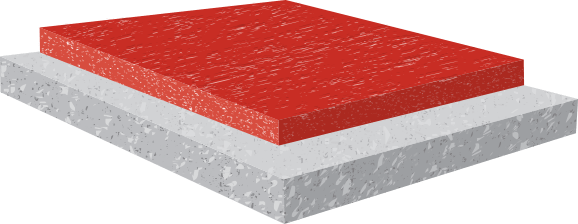